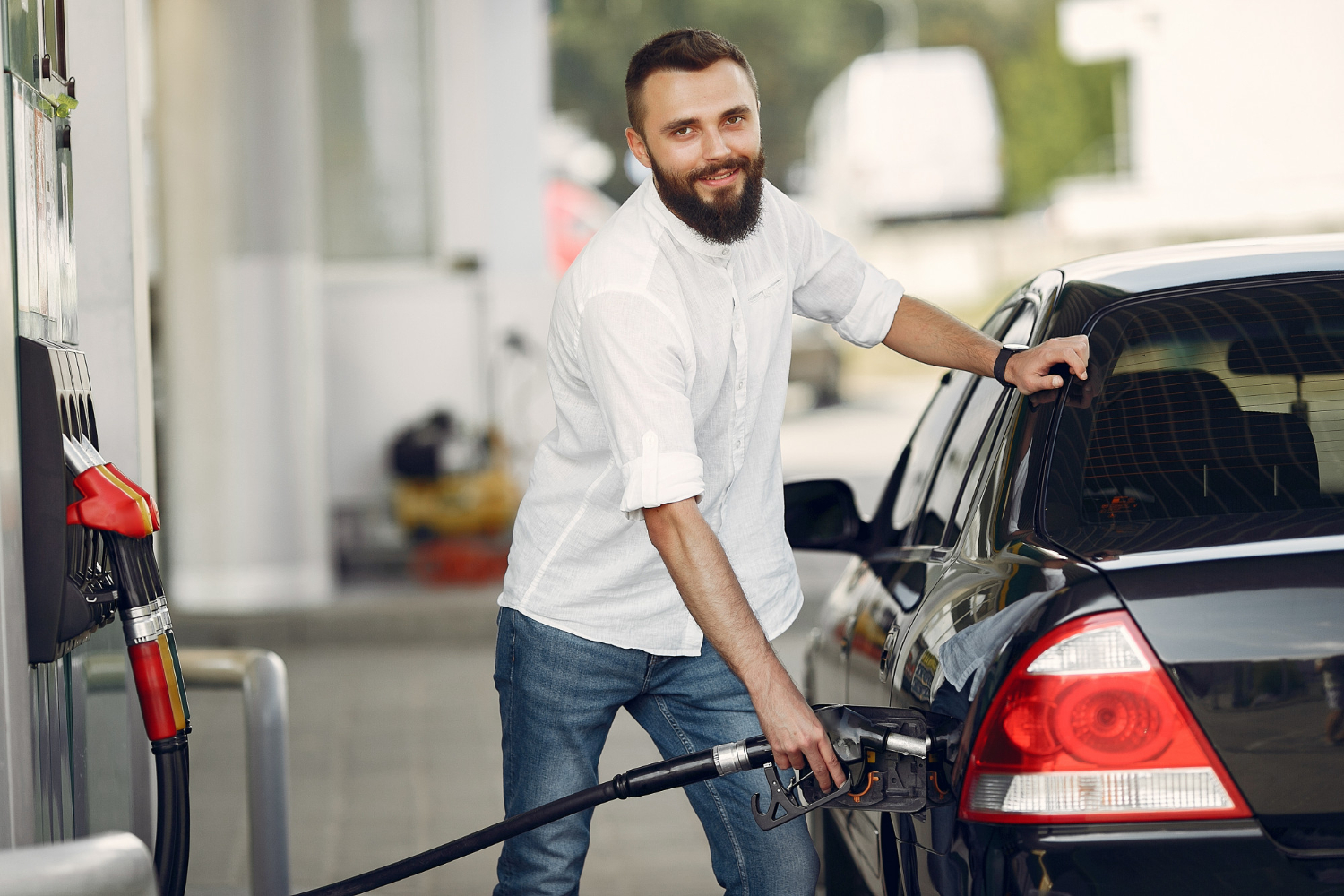
- April 29, 2019
- Commercial, Industrial, Projects
There’s no denying that fuel station maintenance, including the upkeep of pumps, tanks, and other equipment, can be a very taxing process. Like any industry with machinery and complex IT systems, petroleum service companies require a systematic processes of filing maintenance and equipment reports to make sure the site keeps running – but usually these processes are convoluted and time-consuming.
In our experience, site managers often wonder why it’s not easier to pick up on a fault in a fuel pump, and other wetstock management units, before the fault causes serious trouble. Many wish that it was easier to monitor the maintenance of all parts in their site, instead of having to order repairs after a part has already broken.
The slow process of fuel pump maintenance
Generally speaking, there are two main issues that can go wrong with fuel pumps:
- Pump outage —if your pumps are not dispensing fuel, then your site is not able to generate any profit. What’s more, if none of the pumps are working then you’ll have to deal with inconvenienced and grumpy customers. Even if just one pump is down, that’s still fuel that’s not selling.
- Pump is over-dispensing — sometimes, pumps can even be over-dispensing your fuel stock. While customers will think this is great (they get some free fuel, after all), the increased fuel consumption means you could be losing massive amounts of profit – and losing more fuel than your system is tracking. So on top of lost profits, your fuel data is also going to be full of anomalies.
Solving errors or breakages in petrol pump management systems is often painful for site managers because it’s difficult and time consuming to identify the fault. Most sites don’t have instantaneous knowledge when a problem happens, and sometimes the problem will be discovered much later on, when there’s an end-of-day variance or when there’s a negative result on the SIR report. This means that the problem could have been going for days, or weeks, without anyone knowing — that’s a huge loss in fuel and profits!
And even once you’re aware of a problem, there’s still the long process of troubleshooting each and every pump and equipment part to find out where the problem actually is.
And then there’s every site manager’s worst nightmare — the emergency stop. Accidental pressings of the emergency stop occur all the time and it’s very difficult to tell if the emergency is real or not. This is a huge inconvenience when a site-wide shutdown has to take place only for you to later find out that it was all because a kid decided to press a big red button.
How do I gain visibility over my fuel station maintenance?
What every site manager needs is full visibility over their site. When a problem occurs, they need to know about it instantaneously — rather than at the end of the day or in a few weeks’ time. If site managers could identify when and where a problem occurs, they could institute measures to fix the problem straight away and eliminate the process of troubleshooting the equipment. Ultimately, you need a fuel consumption monitoring system that talks to your petrol pump management software, in order to catch those errors early.
Fortunately, gaining visibility over fuel station maintenance is easy with Fuelsuite.
This solution allows you to monitor maintenance process across multiple sites from the comfort of your desk. There are major benefits to this solution:
- Monitor your fuel inventory in real-time — be alerted to dispensation errors in your fuel pumps as soon as they happen.
- Company-wide accurate alerts — both the enterprise and the operator can be notified of a specific hose exhibiting a problem.
- Receive updates on fuel inventory, sales, and equipment every 30 seconds.
- Gain instant knowledge of emergency stop shutdowns and the reasons behind them.
Fuelsuite allows you to be proactive over the maintenance and issues at your sites, giving you the visibility to make wise choices.